métallurgie
(latin scientifique metallurgia, du grec metallourgeîn, exploiter une mine)

Ensemble des procédés et des techniques d'extraction, d'élaboration, de mise en forme et de traitement des métaux et de leurs alliages.
Le traitement des métaux
Introduction
La purification des métaux depuis leur état de minerai, les différents traitements thermiques ou mécaniques qui leur sont appliqués, leur mise en forme par forgeage, laminage ou autres méthodes, l'étude de la genèse et de la structure des alliages, les recherches sur la corrosion ou le recyclage, toutes ces techniques, et les connaissances empiriques et scientifiques qui les sous-tendent, entrent dans le vaste domaine de la métallurgie, dont quelques points essentiels sont présentés ici.
Les minerais contiennent généralement des oxydes ou des sulfures métalliques au sein d'une matrice, la gangue. Une fois celle-ci éliminée, le minerai doit être réduit. Pour le fer, le cuivre, le plomb ou le zinc, la réduction chimique par le monoxyde de carbone se fait à l'intérieur même du haut-fourneau par combustion de coke (charbon pyrolysé). Pour les métaux tels que le molybdène ou le tungstène, la réduction directe par l'hydrogène est un procédé, plus coûteux, qui a l'avantage de donner un métal plus propre. Pour les métaux très électronégatifs, aluminium ou sodium, l'électrolyse est la meilleure méthode.
L'industrie des semi-conducteurs a besoin de silicium pur à 99,999 999 %. Les méthodes de purification chimique étant insuffisantes, seule la technique de fusion de zone réalise cette performance. L'industrie nucléaire a d'autres exigences. La pureté chimique ne lui suffit pas, il lui faut une proportion précise d'isotopes de l'uranium : le combustible nucléaire doit être préalablement enrichi en uranium 235.
Les propriétés mécaniques des métaux purs ne permettraient que peu d'applications. Seule la grande variété des alliages apporte richesse et diversité à la métallurgie. En revanche, les structures engendrées au cours des traitements thermiques sont d'une grande complexité. À l'échelle microscopique, l'arrangement respectif des atomes peut donner naissance à des microdomaines qui expliquent les propriétés macroscopiques des alliages. Récemment, des expériences embarquées dans les stations spatiales comme Spacelab ont montré qu'il était possible de réaliser en microgravité des matériaux aux propriétés nouvelles, ce qui ouvre des perspectives pour des utilisations très spécialisées.
Dates clés de la métallurgie
DATES CLÉS DE LA MÉTALLURGIE | |
Âge du fer | Depuis les temps préhistoriques, les hommes ont appris à utiliser le fer natif (météorites, écorce terrestre) ou à réduire directement des minerais. |
Forge catalane ou bas foyer (minerai et charbon de bois). | |
Premier haut-fourneau. Utilisation du coke. Affinage solide (puddlage)de la fonte ou décarburation dans les forges comtoises. Obtention d'acier par apport de carbone (cémentation de barres de fer puddlé). | |
Âge de l'acier | Production d'acier par fusion de fer puddlé et de fonte, dès |
Temps modernes | Développement de variétés de procédés de soufflage d'air ou d'oxygène. Essor de la fusion électrique par arc ou induction. Dès |
Des métaux et des hommes
Bronze
Le bronze est un alliage de 70-90 % de cuivre et d'étain, éventuellement plomb ou antimoine. Vers 2500 avant J.-C. commence en Europe méditerranéenne l'âge du bronze, ou plutôt l'âge de la métallurgie : fours à 1 100 °C, alliages, recuit, moulage, forgeage.
Fer
Dès le ixe s. avant J.-C. en Europe occidentale, l'âge du fer représente un bond technologique : fours à haute température (1 535 °C), purification, forgeage, fabrication de grandes pièces.
Pour en savoir plus, voir l'article sidérurgie.
Aluminium
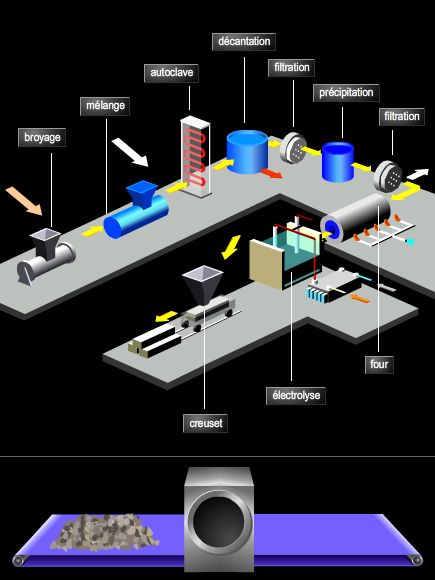
L'élaboration industrielle de l'aluminium, isolé par Œrsted en 1825, a été réussie par Sainte-Claire-Deville (1854). Bien que protégé par Napoléon III qui l'introduisit à la Cour sous forme de couverts, l'aluminium n'a connu de triomphe qu'avec l'électrométallurgie, inventée simultanément en France et aux États-Unis par Paul Héroult et Charles Hall (1886).
Or
L'or est inaltérable et naturellement pur. Les Égyptiens en faisaient des bijoux dès le IIIe millénaire avant J.-C. L'or est thésaurisé sous formes de lingots ou de monnaies. Il sert en orfèvrerie, en dentisterie et à de rares utilisations techniques : vaisseaux spatiaux, contacts électriques, circuits électroniques.
Plutonium
Découvert par G. T. Seaborg à Berkeley (1941), ce métal transuranien fut caché sous le nom de code de « cuivre » (→ plutonium). Il a été révélé au grand public avec la première bombe atomique (1945).
L'élaboration des métaux
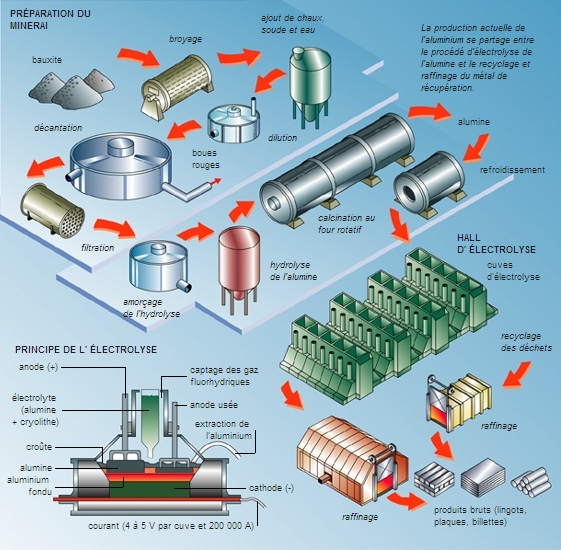
Presque toujours oxydés dans les minerais naturels, les métaux doivent subir une réduction pour passer à l'état métallique. De même qu'ils diffèrent entre eux dans leur affinité à l'oxygène, ils diffèrent dans leur réactivité au cours de la réduction à l'état métallique. Ainsi, l'aluminium métal réduit aisément l'oxyde de fer, car l'affinité de l'aluminium pour l'oxygène est plus grande que celle du fer. (L'inverse n'est évidemment pas vrai : l'aluminium métal ne peut être obtenu à partir d'oxyde d'aluminium et de fer métallique.) Parmi les métaux usuels, l'ordre d'affinité avec l'oxygène croît dans la série cuivre, fer, aluminium, silicium, sodium. Mais un autre élément chimique tient une place particulière : le carbone. Il existe abondamment dans la nature sous sa forme réduite, le charbon ; et, en outre, ses monoxyde et dioxyde (CO et CO2) sont des gaz. La conjonction de ces deux propriétés a été mise à profit dans de nombreux procédés.
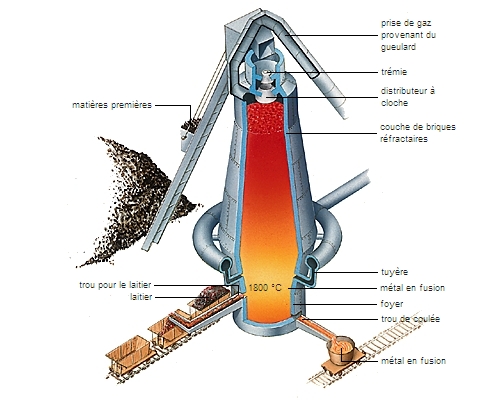
Un procédé technologique ne se résume pas en une équation chimique. Ainsi, celle de la réduction du fer par le coke : 3CO + Fe2O3 + impuretés à 1 000 °C →2Fe + 3CO2 + laitier ne décrit pas vraiment les événements qui se succèdent. La combustion du coke produit à la fois la chaleur et le gaz CO indispensables à la réaction. Le gaz entre beaucoup plus intimement en contact avec le minerai que ne le ferait un solide. Le fer, liquide dense, s'écoule au fond du haut-fourneau, se séparant ainsi des autres produits de la réaction. Le gaz CO2 s'échappe spontanément, et le laitier, liquide peu dense, flotte au-dessus du fer.
Le principe ne change pas quand l'hydrogène est pris comme réducteur à la place du CO. Plus cher, mais aussi exempt d'impuretés, l'hydrogène est utilisé pour la réduction du tungstène et du molybdène. Ce procédé évite la formation des carbures métalliques produits avec tous les procédés au coke, quels qu'ils soient.
L'électrométallurgie est pratiquée, notamment, pour l'élaboration de l'aluminium. L'alumine Al2O3, difficile à réduire par voie chimique, est fondue dans un bain de cryolithe (Na3AlF6), à 960 °C. Au cours de l'électrolyse à faible tension (4 V), l'alumine se décompose ; l'oxygène va vers l'anode en carbone, qui est brûlée (le gaz CO2 est purifié avant d'être rejeté), l'aluminium descend vers la cathode qui forme le fond du creuset. Le courant circulant dans la cellule est de 100 000 A. Pour éviter de changer d'anode tous les mois, l'anode de type Söderberg est coulée et cuite continûment sur place à la température du four. La chaleur dissipée par effet Joule est suffisante pour maintenir le système en fusion, tant qu'il est alimenté en alumine.
L'aluminium est lui-même utilisé pour la réduction de l'oxyde de chrome Cr2O3 (aluminothermie). La réaction très exothermique s'écrit : Cr2O3 + 2Al → Al2O3 + 2Cr.Le mélange d'oxyde de chrome et de poudre d'aluminium est introduit dans le creuset, où est enflammé un ruban de magnésium. La chaleur dégagée suffit à amorcer la réaction, qui continue spontanément. Après refroidissement et solidification, le creuset contient deux couches métalliques qui se séparent facilement : du chrome pur et un mélange Al2O3−Cr2O3. La pureté du chrome dépend de celle de l'aluminium réducteur. Trois tonnes de chrome par cuve sont ainsi obtenues.
Exemples de métallurgies récentes
Deux secteurs technologiques de pointe, l'informatique et l'énergie nucléaire, dépendent chacun d'un métal : le silicium et l'uranium. L'élaboration de ceux-ci présente deux types de difficultés. D'abord, leur grande affinité pour l'oxygène impose des précautions particulières lors de la préparation. Ensuite, l'industrie des semi-conducteurs ne se contente pas de silicium ordinaire : elle exige du silicium ultrapur. Quant aux centrales nucléaires, elles ont besoin d'uranium enrichi, d'une teneur en isotope 235 supérieure à celle de l'uranium naturel. L'élaboration de ces métaux se fait en deux étapes. La première est traditionnelle ; la seconde, plus élaborée, est seule évoquée ici.
La quantité d'impuretés restant dans un échantillon de silicium peut être réduite à 1/10 000 par purification chimique. C'est encore insuffisant pour l'industrie des semi-conducteurs, qui requiert une pureté de l'ordre du milliardième. La fusion par zone permet d'atteindre cette valeur. Un barreau de silicium solide, chimiquement purifié, est chauffé, par induction de courants hyperfréquence ou par bombardement électronique, sur une zone étroite, au-dessus de la température de fusion. Les impuretés migrent dans cette zone liquide, que l'on déplace lentement de la tête à la queue du barreau. Après plusieurs passages, le barreau est ultrapur, toutes les impuretés s'étant rassemblées dans cette queue (de la largeur de la zone fondue), qu'il suffit de couper.
L'uranium à l'état naturel contient 99,3 % d'uranium 238 (non fissile) et 0,7 % d'uranium 235 (fissile). Mais les éléments combustibles chargés dans les centrales doivent avoir une teneur en isotope 235 comprise entre 2 % et 4 %. L'enrichissement consiste à trier deux isotopes aux propriétés chimiques pratiquement identiques, dont les masses ne diffèrent que de 1 %. Par diffusion gazeuse, un composé gazeux de l'uranium, l'hexafluorure UF6, traverse des barrières poreuses, groupées en étages d'enrichissement élémentaire. Le composé de l'isotope 235 les traverse légèrement plus vite que le composé de l'isotope 238. La séparation tient à cette faible différence. L'opération étant répétée en cascade des milliers de fois, le taux d'enrichissement augmente lentement. D'autres procédés sont développés, comme la séparation par laser, ou photo-ionisation sélective (procédé SILVA).
De la cristallographie au traitement thermique des métaux
Les propriétés d'un matériau métallique dépendent largement des transformations qu'il a subies antérieurement. Pour comprendre ce phénomène, il faut descendre à l'échelle atomique. Dans un alliage binaire, les deux éléments peuvent former soit une solution solide, soit des composés définis. Dans les solutions solides, les atomes de l'un des composants pénètrent dans le réseau cristallin de l'autre, ce qui se fait soit par insertion, soit par substitution. Dans le premier cas, les atomes de l'élément de plus petit diamètre se glissent dans les interstices du réseau de l'autre. Tel est le cas de la martensite, constituant principal de l'acier trempé (Fe, C). Dans le second cas, les atomes d'un élément viennent au hasard se substituer à ceux de l'autre dans le réseau. Tel est le cas des alliages cuivre-or, cuivre-platine ou du laiton (cuivre et zinc). Très différents sont les composés définis (ou intermétalliques). Ils se forment lorsque les deux éléments de l'alliage se rencontrent dans des proportions simples, généralement stœchiométriques, et composent ensemble une surstructure cristalline, différente de leurs deux structures initiales. La cémentite, Fe3C, l'une des phases des aciers au carbone, et le laiton β', Cu5Zn8, phase ordonnée, dure et fragile de cet alliage, connu pour sa malléabilité et sa résistance mécanique, en sont des exemples.
Si on refroidit lentement un alliage homogène, stable à haute température, à une certaine température de transition, il devient instable et les atomes se réorganisent en deux phases qui coexistent dans le solide. La diffusion des atomes est d'autant plus lente que la température est basse. Mais, si l'alliage est refroidi brutalement, l'arrangement atomique, qui n'existe en principe qu'à température élevée, persiste à basse température. C'est le phénomène de trempe. Ainsi, au-dessus de 720 °C, le fer et le carbone (0,8 %) forment une solution solide, l'austénite, qui se décompose par refroidissement lent en lamelles alternées de ferrite et de cémentite. La trempe empêche la formation d'agrégats entre ces deux phases ; il se forme instantanément des cristallites de martensite. L'acier est plus dur, mais aussi plus fragile. Le mode de refroidissement, lent ou rapide, affecte profondément la structure et les propriétés d'un alliage.
Au cours du soudage, le métal porté localement au-dessus de la température de fusion présente un fort gradient thermique entre le point chaud et les parties restées froides. Les nouvelles phases qui apparaissent n'ont pas le temps de s'homogénéiser au cours du refroidissement. Les différences locales modifient les propriétés mécaniques du matériau, favorisant, par exemple, ultérieurement la corrosion. La corrosion à haute température peut déjà se produire pendant le soudage. Le soudage à l'argon (gaz inerte) pallie cet inconvénient.
Métallurgie et microgravité
Dans un satellite en vol orbital règne un état de quasi-impesanteur. Il subsiste une certaine microgravité (de l'ordre de 10−5 à 10−6 g), due à la pression atmosphérique résiduelle, aux manœuvres du véhicule, à la stabilisation gyroscopique, etc. Cette quasi-absence de gravité modifie complètement le déroulement de certains processus. Sur Terre, un métal en fusion ne reste pas homogène ; les zones chaudes, moins denses, montent à la surface. Il en résulte un courant de convection qui n'existe pas en microgravité. Les mécanismes d'échange, les forces de cohésion, la surface de séparation entre phases sont changés. En microgravité, un alliage liquide cristallise différemment et forme un matériau aux propriétés nouvelles. Sur l'échantillon d'alliage Al/Cu solidifié en microgravité lors de la mission Spacelab (novembre 1985), les monocristaux d'aluminium pur forment un réseau régulier de dendrites.