charbon
(latin carbo, -onis)

Roche stratifiée combustible, de couleur noire, formée par l'accumulation de débris végétaux transformés par la carbonisation.
CHARBONS
Introduction
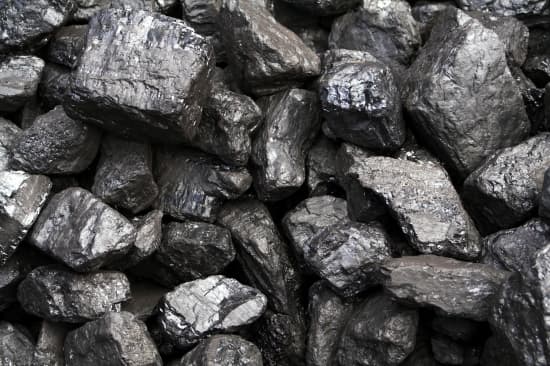
Plus largement répandu et mieux réparti que le gaz et le pétrole, le charbon voit son extraction de plus en plus automatisée, que ce soit en mines profondes ou en mines découvertes. Ennobli sur le site même de la mine par lavage et flottation, le charbon marchand dispose d'une infrastructure sans cesse élargie de transports continentaux (voies ferrées, voies d'eau) et maritimes (ports minéraliers), liée à un important commerce international.
Le charbon fournit 28 % environ de l'énergie primaire consommée dans le Monde et il occupe la première place dans la fourniture mondiale de l'électricité, soit 41 %. Parmi les pays pour lesquels le charbon fournit l'essentiel de la production de l'électricité on peut citer la Pologne, 93 %, l'Afrique du Sud, 93 %, l'Australie, 80 %, la Chine, 78 %, l'Inde,69 %, les États-Unis, 50%.
Le charbon se caractérise aussi par son aptitude à être transformé en coke par le simple effet de la chaleur. Remplaçant du traditionnel charbon de bois, le coke est le réducteur de base des minerais métalliques. Ce sont d'ailleurs les besoins sans cesse croissants de l'industrie sidérurgique qui ont conduit l'industrie cokière à son développement actuel. Les sous-produits de celle-ci ont mis à la disposition des chimistes des hydrocarbures, riches matières de base dont est sortie toute la chimie industrielle moderne. Leur coproduction étant toutefois limitée par celle du coke, ces bases chimiques ont été bientôt produites à partir du gaz naturel et du pétrole sous la pression croissante du marché. Il n'en reste pas moins que la transformation totale du charbon en bases chimiques compétitives, au moyen des techniques de gazéification et de liquéfaction, reste un objectif majeur, pour lequel les technologies industrielles compétitives sont à développer.
Le charbon dans le monde, production et réserves
Si aucun continent n'est totalement dépourvu de dépôts carbonifères, force est de constater que la répartition des ressources est pour le moins hétérogène. Il faut distinguer les ressources, tonnage total du charbon physiquement en place, et les réserves, que l'on classe suivant leur accessibilité, leur coût de revient et leur valeur marchande. Les facteurs techniques et économiques, qui déterminent les possibilités d'exploitation dans de bonnes conditions de rentabilité, entraînent des modifications de la carte des réserves.
La production mondiale de charbon, houille et lignite, est de l'ordre de 6 300 millions de tonnes. Les deux premiers producteurs sont la Chine et les États-Unis avec, respectivement 39 % et 17 % du total mondial. Ils laissent loin derrière les producteurs suivants, l'Inde, l'Australie et la Russie, respectivement 7 %, 6 %, et 5 % du total mondial. Les échanges maritimes concernent environ 12 % de la production.
Dans les conditions techniques et économiques actuelles, les réserves mondiales de charbon représentent 80 % de l'ensemble des énergies fossiles. Sur la base d'une croissance économique modérée, les réserves prouvées planifiables sont estimées suffisantes pour environ 200 ans. Elles sont actuellement évaluées à près de 900 milliards de tonnes (deux tiers pour la houille et un tiers pour le lignite).
40 % des réserves mondiales se trouvent en Asie, essentiellement en Chine (340 milliards de tonnes de houille, 100 de lignite), où l'immense gisement du Shanxi disposerait de près de la moitié des réserves du pays. L'Inde, qui a entrepris la modernisation de ses mines, dispose de 16 milliards de tonnes de réserves prouvées planifiables.
L'Europe de l'Est (avec la Russie et l'Ukraine) représente dans les évaluations actuelles plus du quart des réserves mondiales, mais plus de la moitié de ses ressources est constituée de lignite. Les grands gisements européens de houille, ceux du Donbass en Ukraine et de Silésie en Pologne, exploités depuis très longtemps, sont aujourd'hui confrontés aux problèmes liés à l'approfondissement des gisements et au vieillissement des structures d'exploitation.
L'Europe de l'Ouest ne représente plus que 5 % des réserves mondiales, réparties par moitié entre houille et lignite (ce dernier essentiellement en Allemagne). Les grands bassins houillers de la Ruhr, d'Aix-la-Chapelle - Limbourg, de Sarre-Lorraine, de Wallonie - Nord-Pas-de-Calais, des Midlands, du Yorkshire et du pays de Galles ont déjà été largement exploités.
L'Amérique du Nord renferme un peu plus de 24 % des réserves mondiales prouvées (moitié houille, moitié lignite), essentiellement aux États-Unis. Les bassins riches et réguliers des Appalaches et du Centre-Est, qui assuraient encore récemment presque toute la production, ne représentent que le quart des réserves. L'Amérique du Sud renferme moins de 1 % des réserves prouvées planifiables. La Colombie se singularise par sa politique de développement de gisements charbonniers encore quasi inexploités.
La part de l'Australie et celle de l'Afrique du Sud sont chacune voisines de 5 % des réserves mondiales, mais ces deux pays bénéficient de gisements d'exploitation récente à très bas coût de revient.
L'extraction et la préparation du charbon
Introduction
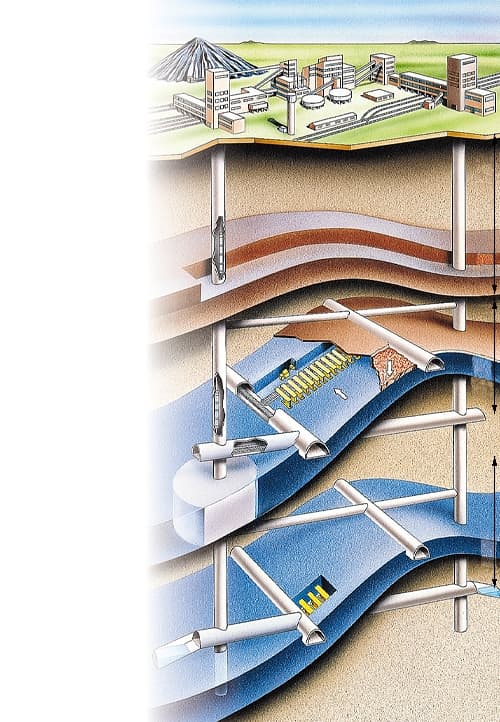
Formé il y a environ 250 millions d'années dans les couches de débris végétaux en décomposition sur lesquelles se sont déposés des sédiments, le charbon est entouré de roches compactes qui ont été plissées, faillées et déplacées par les grands mouvements de l'écorce terrestre. Il est extrait par exploitation souterraine ou à ciel ouvert, le choix étant fonction de la configuration géologique du gisement et de son environnement.
L'exploitation à ciel ouvert
C'est le mode d'exploitation choisi lorsque les terrains stériles, les morts-terrains, qui recouvrent le charbon ont une faible épaisseur. Ces mines découvertes évoquent de gigantesques amphithéâtres qui peuvent atteindre plusieurs kilomètres de diamètre et plusieurs centaines de mètres de profondeur. Après déblaiement des morts-terrains, le charbon est enlevé par niveaux horizontaux successifs. Les avantages sont nombreux : productivité, faible prix de revient, délai réduit de mise en production, souplesse de gestion. Apparenté aux travaux de terrassement, ce procédé fait intervenir des engins puissants : roues-pelles, foreuses, chargeuses, pelles hydrauliques. L'exploitation est arrêtée lorsque la quantité de stériles à déplacer est de 10 à 15 fois supérieure à celle du charbon extrait. Le site est alors remblayé et le paysage, reconstitué. Ce type d'exploitation est très développé dans les grands pays producteurs : États-Unis, Canada, Russie.
L'exploitation souterraine
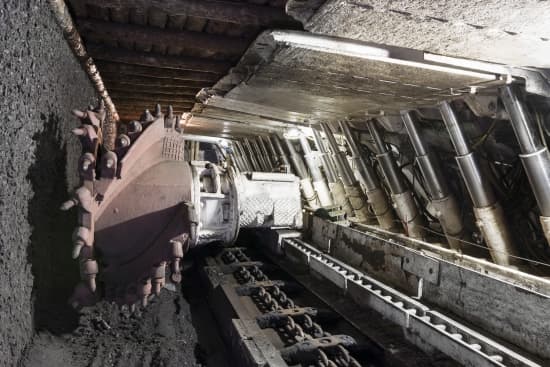
Elle est mise en œuvre lorsque les gisements sont situés à une profondeur supérieure à 1 000 m. Le charbon est extrait à partir de puits verticaux ou de plans inclinés, les descenderies, reliés à différents niveaux, ou étages, par un réseau de galeries d'infrastructure : plusieurs dizaines de kilomètres pour des sections de 10 à 20 m2. Aux endroits où ces galeries rencontrent le gisement de charbon, des voies sont creusées dans la veine, entourant le panneau à exploiter. La taille est alors ouverte entre deux voies sensiblement parallèles, distantes d'une centaine de mètres ; elle progresse par abattage de tranches successives perpendiculaires aux deux voies sur des longueurs de plusieurs centaines de mètres. Le charbon est remonté au jour dans des cages d'acier, ou skips, qui peuvent contenir plus de 20 tonnes de produits. Abattage, transport, pilotage des ventilateurs et des pompes s'automatisent de plus en plus, par utilisation de matériel électrique fonctionnant en ambiance hostile (température, humidité, vibrations, risque d'explosion).
Lavage et calibrage
Le charbon brut contient généralement des stériles, impropres aux utilisations ultérieures. Il est alors acheminé dans un lavoir, où il est immergé dans un liquide dense composé d'eau et de fines particules de magnétite en suspension. Les déchets lourds sont précipités au fond du bac ; le charbon plus léger flotte à la surface, où il est récupéré. Pour les produits plus fins, des pulsations mécaniques provoquent la séparation des particules de charbon et de schiste. Les charbons récupérés sont alors calibrés, chaque calibre correspondant à un usage spécifique.(→ houille.)
La cokéfaction
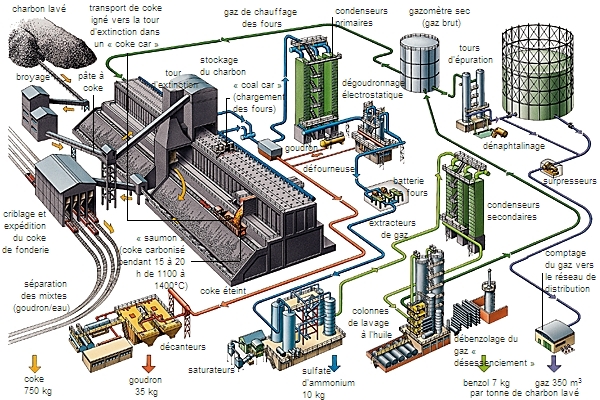
Réducteur chimique et base énergétique pour la production de la fonte et de nombreux autres métaux non ferreux, comme le plomb et le zinc, le coke est fabriqué dans de grandes unités modernes d'une capacité supérieure à une mégatonne par an. Celles-ci sont soit intégrées dans un complexe sidérurgique, généralement situé en bord de mer (en France : Fos-sur-Mer ou Dunkerque, cokeries sidérurgiques de la société Sollac), soit installées sur le carreau d'une mine (en France : Carling, cokerie minière des Houillères du bassin de Lorraine).
La cokéfaction est une opération chimique discontinue et fort complexe. Chauffée jusqu'à 1 000 °C, la poudre de pâte à coke (mélange de plusieurs charbons) est transformée par fusion en un solide poreux et fissuré, le coke, après passage par une phase plastique (magma) et libération d'une quantité de bulles de gaz qui se forment par décomposition chimique. Ce départ d'environ 25 % de matières volatiles s'accompagne d'un important retrait de matière, le solide fondu se fragmentant en une multitude de morceaux de forme et de taille différentes. Ce morcellement irrégulier du coke favorise notablement la circulation des gaz lorsqu'il est entassé dans le haut-fourneau. Ainsi joue, dans ce réacteur de réduction, le phénomène de perméabilité au gaz des lits de solides.
Dans une cokerie moderne, quelque 5 000 tonnes de pâte à coke entrent chaque jour dans la batterie des fours à coke, la pâte étant elle-même préparée à partir d'un stock de 5 à 10 tas de 50 000 t de différents charbons commerciaux. Ceux-ci passent par une section automatisée de manutention et de transfert, où ils sont entreposés, dosés et où les noix et les fines de charbon sont rebroyées. Pour ménager l'environnement et empêcher l'envol de poussière sous l'effet du vent, les tas de charbon sont fixés par arrosage avec des solutions aqueuses de latex. La pâte à coke ayant été préparée, elle est chargée par lots de 50 à 55 t dans des fours parallélépipédiques d'un volume utile de 70 m3 (L = 17 m, l = 0,55 m, h = 8 m). Entre deux fours est intercalé un compartiment commun de chauffage, le piédroit. Fours et piédroits sont alternés en batteries de quelque 70 fours, fonctionnant en continu sur un cycle de cuisson. La durée de celui-ci varie entre 16 h, pour produire du coke de haut-fourneau, et 36 h pour du coke de fonderie. Chaque four se trouve dans un état d'avancement de cuisson différent. Toutes les étapes de la carbonisation s'échelonnent donc sur l'ensemble des fours de la batterie. Ainsi, les opérations qui suivent la collecte centralisée des gaz de distillation entrent dans un processus continu. Fortement refroidi à l'entrée du collecteur (le barillet) par aspersion abondante d'eau froide pulvérisée, le gaz brut de pyrolyse abandonne la quasi-totalité de ses hydrocarbures lourds, les goudrons. Le rendement de cette séparation est de 3 à 4 %.
Les hydrocarbures légers sont récupérés par lavage sélectif à l'huile ; on en extrait ensuite le benzol (mélange de benzène, toluène et xylènes) par réchauffage avec un rendement de 1 à 1,5 %. Dégoudronné et désessencié, le gaz permanent (c'est-à-dire restant dans cet état à température ambiante) subit alors un traitement pour séparation de l'ammoniac et de l'hydrogène sulfuré. Il est ensuite envoyé dans le réseau de gaz, mais il peut aussi servir de base chimique pour l'extraction de l'hydrogène. Pour 1 Mt de coke, la cokerie de base produit simultanément environ 500 millions de m3 de gaz à 60 % d'hydrogène, 50 000 t de goudrons et 15 000 t de benzol.
Les transformations chimiques du charbon
Introduction
L'extraction de nombreux produits chimiques à partir du charbon brut peut se faire par différents procédés, dont certains ne gardent qu'une importance historique. Si la cokéfaction implique généralement le mélange de divers charbons en une pâte fusible qui se resolidifie en coke, la pyrolyse sélective des charbons est effectuée sur une espèce unique de charbon non fusible (c'est-à-dire non agglutinant).
La pyrolyse
Appelée dévolatilisation quand le charbon de départ est riche en matières volatiles (lignites et flambants) et calcination quand celui-ci est, au contraire, pauvre en matières volatiles (anthracites et maigres), la pyrolyse industrielle relève de types de procédé adaptés aux diverses granulométries des charbons : réacteur en lit fluidisé pour les poudres, réacteur à sole ou en cylindres tournants pour les grains, réacteur à cuve, continu ou discontinu, pour les charbons calibrés. Produisant quelques dizaines de millions de tonnes de cokes spéciaux dans des ateliers de faible taille unitaire (de quelque 10 000 t/an à 200 000 t/an), l'industrie de la pyrolyse alimente l'électrométallurgie en carbone réducteur et les industries des matériaux en matière première. Comme ces cokes spéciaux se substituent avantageusement à la traditionnelle fabrication de charbon de bois, ils contribuent à la sauvegarde du patrimoine forestier. Ainsi, les cokes de lignite se substituent aux charbons de bois pour la purification des eaux usées ou des gaz industriels. Par pyrolyse sélective, les structures phénolées complexes, issues de la lignine des végétaux houillifiés, sont partiellement dépolymérisées en molécules phénoliques de base : phénol, crésols et surtout xylénols. D'abord condensées du gaz brut de pyrolyse sous forme de goudrons noirs à forte odeur, ces molécules – qui sont à la base d'une branche intégrée de l'industrie chimique – sont séparées par distillation sélective en produits de qualité commerciale. Elles sont ensuite transformées en antioxydants, insecticides, fongicides et résines formophénoliques.
Produisant les goudrons phénolés primaires avec un rendement industriel d'environ 10 % par rapport au charbon de départ, la pyrolyse ne leur fait pas subir de dégradation thermique ultérieure ; elle respecte donc leur structure aromatique. Cette pyrolyse ménagée opère à température relativement basse (500 °C à 800 °C), sans risque d'une surchauffe qui ferait craquer les gaz primaires de dévolatilisation. Elle se distingue donc de la cokéfaction, opération au cours de laquelle les goudrons primaires sont craqués en goudrons secondaires au contact des parois très chaudes (avec un rendement de 3 % par rapport au charbon).
La gazéification
La combustion partielle du charbon (sous défaut d'air) transforme ce solide en un mélange gazeux de monoxyde de carbone et d'hydrogène. Ce gaz à l'eau, ou gaz de synthèse, se transforme, sous pression et en présence de catalyseurs, en hydrocarbures (procédé Fischer-Tropsch de fabrication de carburants) ou en d'autres molécules recherchées telles que le méthanol. Cette gazéification du charbon, plus coûteuse que celle des produits pétroliers, a été pratiquée en économie de guerre (Allemagne, 1939-1945) et a été adaptée aux conditions économiques particulières de la République d'Afrique du Sud dans le complexe chimique du Sasol. En dépit de nombreux essais de modernisation à l'occasion des chocs pétroliers de 1973 et de 1979, la gazéification du charbon ne s'est pas implantée à ce jour dans les pays à économie de marché.
L'hydrogénation
Un autre procédé, utilisé pendant la Seconde Guerre mondiale, a été l'éclatement contrôlé par hydrogénation de la matrice polymérique du charbon en molécules plus petites. Ici aussi, malgré les très importants efforts d'innovation qui ont suivi les deux crises pétrolières de 1974 et 1978, ce procédé n'a pu être adapté aux conditions économiques actuelles.
La liquéfaction
Imaginée dès 1913 (Bergius, Allemagne), la liquéfaction du charbon a été mise en œuvre en Allemagne pendant la Seconde Guerre mondiale et plus récemment en Afrique du Sud (usines Sasol) ; cependant,les rendements restent faibles et les techniques peu fiables. On distingue : 1° les procédés d'hydrogénation indirecte, utilisant les produits de la gazéification pour fabriquer par synthèse des hydrocarbures liquides ou gazeux ; 2° les procédés d'hydrogénation directe, basés sur une réaction directe de l'hydrogène sur le charbon, en général avec un catalyseur, en phase gazeuse ou liquide. Toutes les recherches en cours portent sur ces procédés, souvent en phase liquide.
GÉOLOGIE
La nature des végétaux et le degré de transformation déterminent les différents types de charbons : boghead, tourbe, lignite, houille, anthracite. Les constituants pétrographiques du charbon sont : le fusain, le durain, le clarain, le vitrain. Ce sont des macromolécules complexes résultant d'une transformation progressive de la cellulose et de la lignine en acides humiques, puis en bitumes, par élimination de l'oxygène.