acier
(bas latin aciarium, du latin classique acies, pointe)

Alliage de fer et de carbone contenant moins de 1,8 % de carbone, susceptible d'acquérir, par traitement mécanique et thermique, des propriétés très variées.
ARCHITECTURE
L'acier dans la construction
Après 1889 (date d'une Exposition universelle, à Paris, qui marque le chant du cygne du « siècle du fer »), le fer riveté, découpé, orné va être remplacé par l'acier, d'abord pour l'ossature enrobée des gratte-ciel ou pour armer le béton. L'emploi pour les ponts est autorisé en 1891 : Louis Jean Résal l'utilise laminé, au pont Mirabeau (1894), et moulé, au pont Alexandre-III (1898), à Paris.
L'obtention des aciers spéciaux et inox (1927) et l'assemblage par soudage autogène (1928) débouchent, grâce à un gain en poids et en main-d'œuvre, sur une expression architecturale où le métal et le verre expriment leur rigueur, depuis la maison du peuple de Clichy (Beaudouin et Lods, 1937) jusqu'au centre Pompidou et au courant high-tech. Avec Mies van der Rohe ou J. Prouvé, l'acier a conquis une place importante dans la construction des grands immeubles. Plus spécifiques encore sont les nappes, planes ou courbes (l'Américain R. B. Fuller), et les structures tendues, appliquées par René Sarger au pavillon français de l'Exposition de Bruxelles (1958).
HISTOIRE
Au xiiie s. apparaissent les premiers hauts-fourneaux (pays de Siegen) et la fonte, dont le moulage prend de l'extension au xve s. À la fin du xviiie s., les métallurgistes anglais appliquent à grande échelle le procédé d'obtention d'acier fondu au creuset pour la confection d'outils et inventent le puddlage (Henry Cort). La seconde moitié du xixe s. voit la découverte et l'essor des grands procédés métallurgiques pour la sidérurgie : procédé Bessemer de convertissage de la fonte en acier (1855) ; procédé Martin d'affinage de l'acier au four à réverbère (1865), amélioré par le système de récupération thermique des frères Siemens ; procédé de convertissage de Thomas et Gilchrist (1878) en milieu basique, permettant de traiter des minerais phosphorés. Durant cette même époque se développent les fours électriques à électrodes (Héroult, en 1900) ; les fours à électrolyse ignée pour la fabrication de l'aluminium, étudiés par Sainte-Claire Deville; les fours à résistance ; enfin, les fours à induction à basse et à haute fréquence. La connaissance des métaux et des alliages prend un caractère théorique et scientifique avec les travaux de Réaumur (1722) ; mais c'est à la fin du xixe s. et au début du xxe s. que la science métallographique se développe, grâce à Osmond, Werth, Le Chatelier, Chevenard, Guillet, Chaudron en France, Roberts-Austen, MacCance en Angleterre, Martens, Maurer en Allemagne, etc. Les phénomènes de traitement thermique sont mieux connus, et de nouveaux alliages sont créés.
La préparation de métaux de plus en plus purs progresse au xxe s. grâce à de nouvelles méthodes de raffinage : méthodes physiques (sublimation, distillation), méthodes chimiques (procédés Mond, Van Arkel, Kroll), méthodes électrochimiques (cuivre et aluminium). On élabore des matériaux d'une pureté ultime (silicium, germanium, notamment) grâce à la méthode de la fusion de zone mise au point par W. G. Pfann.
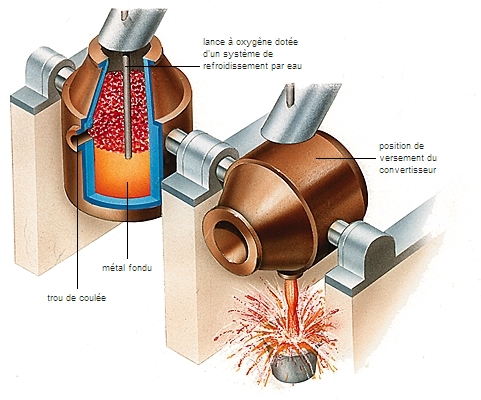
La sidérurgie a connu, un siècle après sa première révolution, une deuxième période de transformation rapide et profonde avec l'apparition du soufflage avec de l’air enrichi en oxygène, aujourd’hui universellement employé. Il permet le traitement de grandes capacités de fonte et l’élaboration d’aciers de haute pureté.
TECHNIQUE
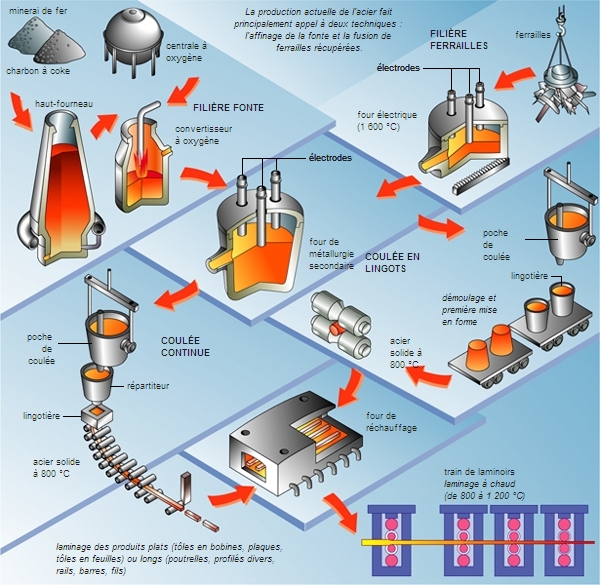
L'acier est élaboré en majeure partie par affinage de la fonte, mais aussi par refusion de ferrailles récupérées et, en quantité limitée, par réduction directe du minerai. (→ sidérurgie).
La structure et les propriétés des aciers dépendent de la teneur en carbone, de la présence ou non d'éléments d'addition (aciers alliés, aciers ordinaires) et des traitements thermiques (trempe, recuit, revenu) ou physico-chimiques subis. À l'état recuit, la constitution des aciers est donnée par le diagramme fer-carbone (→ fer). La ferrite (solution solide très limitée de carbone dans le fer α) est un constituant malléable et de faible dureté des aciers à bas carbone (0,10 %). Quand la teneur en carbone croît, il apparaît de la perlite, constituée de ferrite et de carbure de fer Fe3C, très dur (cémentite). Par trempe directe des aciers ordinaires, on ne peut maintenir à température ambiante l'austénite (solution solide de carbone dans le fer γ) ; il se forme un constituant métastable très dur, la martensite : l'acier devient dur mais peu déformable et fragile. Par revenu, la martensite se décompose en un agrégat très fin, la sorbite, formé de ferrite et de cémentite. Par trempe atténuée ou isotherme, on obtient d'autres constituants : la troostite et la bainite. Les aciers sont utilisés à partir de lingots soit sous forme moulée (fonderie), soit sous forme de produits obtenus par mise en forme mécanique (acier forgé, laminé, filé, étiré, tréfilé, embouti, estampé, fritté, etc.).
Suivant la composition chimique, on distingue deux grands groupes de nuances d'acier : les aciers ordinaires, non alliés (teneur en carbone inférieure à 1 %), et les aciers alliés, subdivisés en aciers faiblement alliés (aucun élément d'addition n'atteint 5 %) et aciers fortement alliés, ou aciers spéciaux (un élément a une teneur supérieure à 5 %). Les éléments d'addition entraînent des modifications de structure (nickel et manganèse élargissent le domaine de l'austénite, chrome et silicium celui de la ferrite), de constitution chimique (tungstène et vanadium, à forte teneur, forment des carbures), de diagramme d'équilibre (ce qui joue un grand rôle pour les traitements thermiques).
Le nickel à faible teneur (0,5 à 5 %) améliore la trempabilité et augmente les caractéristiques mécaniques ; à forte teneur (jusqu'à 50 %), il favorise la tenue à la corrosion. Le chrome (de 1 à 6 %) favorise trempabilité et caractéristiques mécaniques ; de 10 à 20 %, il rend l'acier inoxydable et à 25 % le rend réfractaire. Le silicium (jusqu'à 2 %) augmente l'élasticité et la résilience (ressorts) et diminue les pertes magnétiques (tôles de transformateurs). Le manganèse à 2 % favorise la trempe (acier indéformable) et à 13 % donne une remarquable tenue au choc et à l'usure. Le tungstène (jusqu'à 18 %) forme des carbures durs conférant une grande résistance à l'usure.
Les grandes classes d'application des aciers sont : les aciers de construction (aciers ordinaires ou plus souvent alliés au chrome, nickel, molybdène) ; les aciers à outils ; les aciers inoxydables, classés selon leur structure en aciers martensitiques, (0,4 % C et 12 à 16 % Cr), aciers ferritiques (< 0,3 % C, 16 à 30 % Cr) et aciers austénitiques (18 % Cr, 8 % Ni, < 0,10 % C) ; les aciers réfractaires, présentant une grande résistance à l'oxydation, à la corrosion et au fluage, et, pour des applications particulières, les aciers à roulement (2 % Cr) et les aciers à aimants permanents (jusqu'à 30 % de cobalt, avec additions de tungstène et de chrome).
Production
La production mondiale avoisine aujourd'hui 1,34 milliard de tonnes. Elle a plus que sextuplé depuis la Seconde Guerre mondiale, mais la progression est fortement ralentie depuis le milieu des années 1980, en rapport avec la conjoncture économique, l'essor aussi de produits de substitution plus légers comme l'aluminium ou les plastiques. Cinq pays (Chine, Japon, États-Unis, Russie et Allemagne) assurent plus de la moitié de la production mondiale, mais ce ne sont pas, à l'exception peut-être de la Chine, les plus dynamiques. Les années 1970 et 1980 ont vu surgir de nouveaux producteurs, asiatiques (la Turquie, Taïwan et surtout la Corée du Sud) ou sud-américains (Brésil surtout). Cette mutation (partielle) de la géographie de la production est liée à l'évolution des conditions de production.
Utilisatrice de matières premières pondéreuses (essentiellement minerai de fer et coke ou charbon), nécessitant de lourds investissements, la sidérurgie s'est d'abord implantée sur ou à proximité des gisements (sur le charbon dans les Appalaches et dans la Ruhr, sur le fer en Lorraine). Le développement des transports de masse, surtout maritimes, l'évolution des techniques de production, l'utilisation de minerais de fer de plus en plus riches ont facilité une diversification spatiale, profitant essentiellement aux sites littoraux, ce que l’on appelé la sidérurgie sur l’eau, se substituant parfois aux centres anciens et entraînant alors le déclin de vieilles régions industrielles, comme celles précédemment citées. Plus généralement, les gains de productivité ont, partout, provoqué de sérieuses compressions d'effectifs. Début 2008 ont été lancés les premiers contrats sur l’acier par des marchés à terme, en dépit de l’hostilité des producteurs, ArcelorMittal, premier producteur mondial, en tête.