ciment
(latin caementum, pierre non taillée)

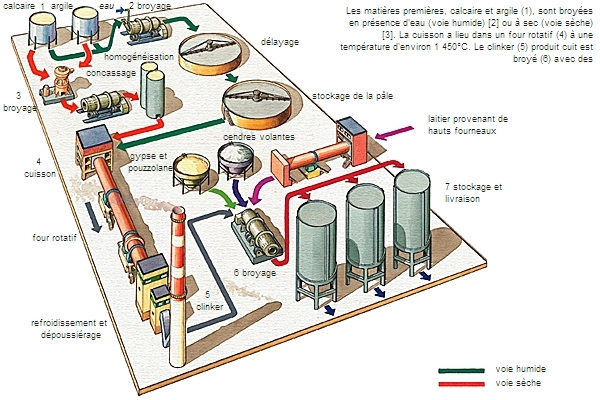
Matière pulvérulente formant avec l'eau, ou une solution saline, une pâte plastique liante, susceptible d'agglomérer, en durcissant, des substances variées.
GÉOGRAPHIE
La production mondiale de ciment est de l'ordre de 2 800 millions de tonnes. La Chine en assure à elle seule environ la moitié ; viennent ensuite l'Inde, le Japon, et les États-Unis.
MATÉRIAUX
Historique
C'est au xviiie s. qu'ont été fabriquées les premières chaux hydrauliques proches des ciments modernes. En 1759, l'Anglais John Smeaton produit un mortier aussi dur que de la pierre en mélangeant des chaux hydrauliques et des cendres volcaniques. Le Français Louis Vicat découvre en 1817 les principes chimiques des ciments et définit les règles de fabrication du ciment hydraulique. Il est considéré comme l'inventeur du ciment moderne.
L'Anglais Joseph Aspdin fait breveter en 1824 le ciment Portland, obtenu à partir d'un procédé de calcination combinant la cuisson de calcaire et d'argile dans des fours alimentés au charbon. La dénomination Portland, due à la similarité de couleur et de dureté avec la pierre de Portland (au sud de l'Angleterre), est à l'heure actuelle toujours employée dans l'industrie.
À la fin du xixe s., le béton moderne à base de ciment Portland devient un matériau de construction largement répandu. De nombreux perfectionnements sont apportés au cours du xxe s. à la fabrication du ciment, notamment avec la production des ciments spéciaux, sans toutefois modifier les caractéristiques physico-chimiques et les propriétés fondamentales du ciment Portland.
Fabrication
D'un emploi devenu quasi universel, le ciment Portland s'obtient en cuisant à haute température un mélange artificiel, parfaitement homogénéisé et dosé, de calcaire et d'argile, et en broyant finement avec du gypse le clinker ainsi obtenu.
La fabrication utilise environ trois fois plus de calcaire que d'argile. Le calcaire provient de carrières ; une fois extraite la roche est chargée et convoyée jusqu'au concasseur. Premier stade du broyage, le concassage réduit les blocs de roche en fragments ne dépassant pas une dizaine de centimètres. Comme il est nécessaire d'obtenir un mélange intime et homogène des constituants, calcaire et argile, ceux-ci peuvent être soit broyés à sec, ce qui nécessite un séchage préalable ou simultané, soit délayés ou broyés, suivant leur dureté, en présence d'eau. Il existe d'autres procédés, dérivés des deux précédents, qui aboutissent tous à une réduction de la matière en grains de dimensions inférieures au dixième de millimètre. Le mélange est cuit jusqu'à une température de l'ordre de 1 450 °C, qui assure la combinaison intégrale de la chaux avec la silice, l'alumine et l'oxyde de fer. La cuisson se fait généralement dans d'immenses fours rotatifs, pour des productions de l'ordre de 1 000 à 3 000 t par jour. Le clinker refroidi, puis broyé avec une petite quantité de gypse (destiné à régulariser la prise) dans d'énormes broyeurs à boulets, est amené ainsi à une très grande finesse.
Les différents ciments
Différents types de ciment permettent aujourd'hui de répondre à la multiplicité des contraintes d'utilisation. Le ciment Portland composé est constitué de clinker broyé avec des cendres volantes. Le ciment métallurgique (appelé aussi ciment de haut-fourneau) est un mélange de clinker broyé avec du laitier granulé. Les ciments composés sont constitués de clinker, de cendres volantes et de laitier de haut-fourneau. Enfin, des ciments spéciaux offrant une meilleure résistance aux sulfates ou à teneur limitée en alcalis sont utilisés pour la fabrication de béton soumis à des conditions d'exploitation particulièrement dures.